Using traditional welding methods, rocket engine nozzles and combustion chambers are some of the most difficult parts to fabricate, requiring up to a year to produce a single part. Now, however, the U.S. National Aeronautics and Space Administration (NASA) is using additive manufacturing technology, also known as 3D printing, to additively build those parts, layer upon layer. This technology differs completely from traditional manufacturing methods that manufacture destructively by taking away material until a final geometry is realized. 3D printing has allowed NASA to produce rocket engine nozzles with integrated cooling channels in 30 days by way of an additive process called blown powder directed energy deposition (BP-DED). See also: Nozzle; Rocket propulsion; 3D printing
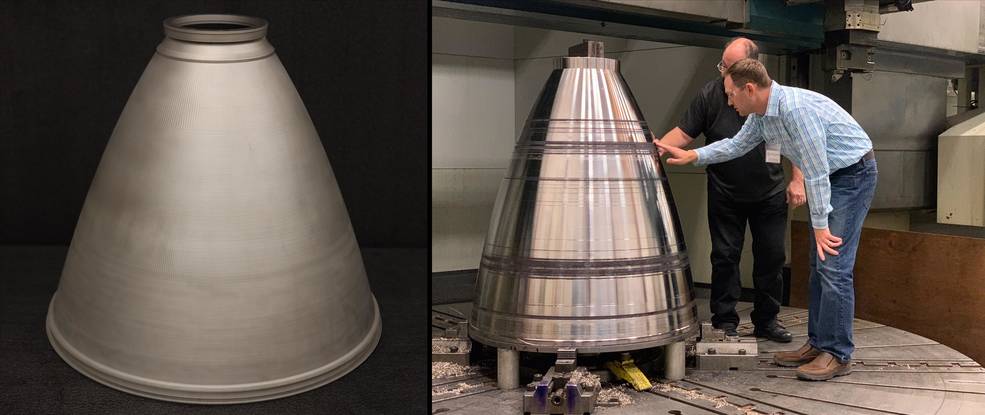
In the BP-DED process, heat energy from a laser melts a metal powder, such as a nickel-iron alloy, as the powder is deposited in layer-by-layer fashion to form the part. In a more traditional manufacturing process, a layer of fine metal powder would be deposited, and then the entire layer would be melted. Also, the BP-DED process can use larger-sized particles than traditionally has been possible, which, in turn, produce thicker layers, resulting in faster production times and allowing for the printing of larger part sizes. With the BP-DED method, all of the components for printing metal powder are integrated into a print head attached to a computer-controlled robotic arm. During printing, the print head uses an inert gas, such as argon or nitrogen, to blow the metal powder into a laser-heated pool of molten metal as the print head advances to additively print layer-upon-layer of metal. See also: Alloy; Laser; Welding and cutting of materials
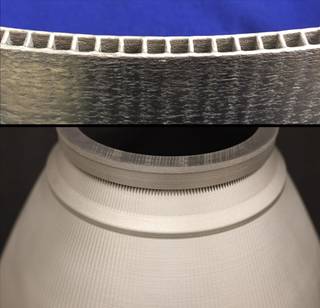
At present, the only size limitation of the BP-DED method is the size of the room in which parts are built. In addition to reducing the build time, the BP-DED method is also reducing the cost for producing parts. As soon as the nozzles produced by BP-DED are certified for space flight, NASA plan to build channel-cooled nozzles up to 1.5 meters (5 feet) in diameter and 2 meters (7 feet) tall for missions to the Moon and Mars. See also: Mars; Moon; Robotics; Space flight
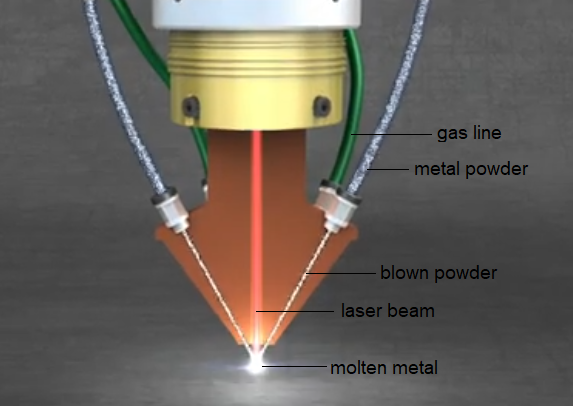