Wood–plastic composite (WPC) lumber has been marketed as a low-maintenance, high-durability product. Retail sales in the United States were slightly less than $1 billion in 2008. Applications include decking, railing, windows, doors, fencing, siding, moldings, landscape timbers, car interior parts, and furniture. The majority of these products are used outdoors and thus are exposed to moisture, decay, mold, and weathering. WPCs are composites made primarily from wood- or cellulose-based materials and plastic(s). The wood utilized is usually in particulate form, such as wood flour or very short wood fibers. Because of the thermal stability of wood, only thermoplastics that melt at temperatures equal to or below 200°C (392°F), which is the degradation point of wood, are utilized in the production of WPCs. The most common plastics used for WPCs are polyethylene (PE), polypropylene (PP), and polyvinyl chloride (PVC). The WPC blends can vary in percentage, with wood content up to 70%, but 50% wood/50% plastic is common. It was first thought that mixing plastic and wood together would result in plastic encapsulation of wood, thereby preventing both moisture sorption and fungal decay. However, after over a decade of use in outdoor exposure, issues have surfaced that are caused by wood decay, susceptibility to mold, and polymer degradation. After the first-generation products showed these problems, the industry began to address the performance issues by improving the formulations with additives, including fungicides, mildewcides, and photostabilizers. Further improvements are continually being investigated today. Researchers around the globe are currently working on understanding the fundamental mechanisms of degradation and on ways to improve WPCs.
Moisture
Moisture is required for biological decay of wood. Air-dried wood should have no more than 20% moisture by weight to resist decay. If free water is added to attain 25–30% moisture content or higher, decay will occur in nondurable species. Wood can also be too wet for decay because there is not enough air for the fungi to develop.
The overall uptake of moisture in WPCs is relatively slow compared to solid wood, and the amount of moisture absorbed by WPCs can vary widely as a result of the influences of the wood flour content, wood particle size, processing methods, and additives. However, moisture uptake in the outer 5 mm (0.2 in.) of WPC commercial products has been shown to be sufficient for fungal attack to occur. Water evaporation from the WPC is also very slow because the plastic inhibits moisture movement, thus providing an opportunity for biodegradation to occur. Laboratory research and field evaluations indicate that WPCs absorb moisture to the point where they can be degraded by fungi.
There are different ways to produce WPCs. The three most common ways are extrusion, compression molding, and injection molding. WPC processing methods influence the moisture sorption, thus making them more or less susceptible to decay. Extruded composites absorb the most moisture, compression-molded ones absorb less, and injection-molded ones absorb the least (Fig. 1). A thin, polymer-rich surface layer forms in injection-molded composites. In addition, higher pressures are used in this process, resulting in the collapse of the wood fiber bundles, which makes a higher-density composite compared with extrusion and compression molding. The amount of moisture absorbed is also influenced by wood particle size and additives. Another variable is whether the WPC is extruded as a solid or a hollow profile. A hollow profile will create a larger surface area that allows for moisture sorption.
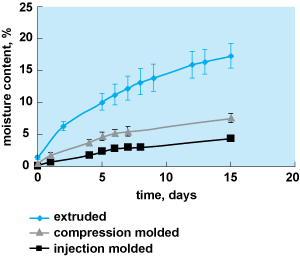
The hydroxyls (chemical groups in which oxygen and hydrogen are bonded and act as a single entity) of wood are primarily responsible for water sorption, which leads to wood swelling. This then can lead to warping and expansion. When WPCs are exposed to moisture, the wood fibers swell, causing stress that can result in damage to the matrix (for example, microcracks), fracture of the wood particles due to restrained swelling, and ultimately interfacial breakdown. For solid wood, moisture alone reduces the strength and stiffness. However, fungal decay reduces these measures by the greatest amount. The mechanical properties of WPCs are more severely affected by moisture absorption than by fungal colonization. The microcracks in the matrix and the damage to the wood particles cause a loss in elasticity and strength.
Decay
Fungi have four basic growth requirements: food (for example, wood, which contains hemicellulose, cellulose, and lignin), moisture (above the fiber saturation point; about 30% moisture content), proper temperature [10–35°C (50–95°F); optimum: 24–32°C (75-90°F)], and oxygen (from the air).
Currently, the indicator of decay in laboratory testing of WPCs is by weight loss using solid wood standards. The soil-block test [American Society for Testing and Materials (ASTM) D 1413 or ASTM D 2017] is utilized in North America, and the agar-block test [European Standards (EN) 113] is used in Europe. In both types of tests, WPC specimens are exposed to a single fungus (either white-rot or brown-rot) and then mass loss of each specimen is calculated in percent, based on initial dry mass. Because WPCs vary in their percentage of wood content, the weight losses can be very low (Fig. 2). The test fungi commonly used are the brown-rot fungi Gloeophyllum trabeum and Poria placenta, and the white-rot fungus Coriolus versicolor.
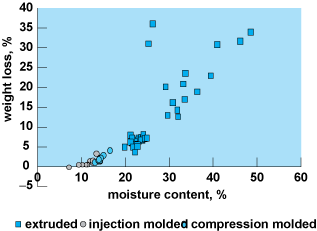
Mechanical property losses can be used to evaluate decay specimens. Both three-point bending tests and dynamic mechanical analysis (DMA) have been utilized. Weight loss is a more sensitive indicator of fungal decay than flexural strength testing, except when using WPCs with high wood contents (for example, 70%).
Laboratory decay testing is helpful in predicting the long-term durability of WPCs, but field studies are needed to verify overall performance. Field exposure can encompass deterioration caused by moisture, fungi, ultraviolet (UV) light, wind, temperature, freeze/thaw cycling, wet/dry cycling, termites, and mold for both aboveground specimens (Fig. 3) and in-ground specimens (Fig. 4).
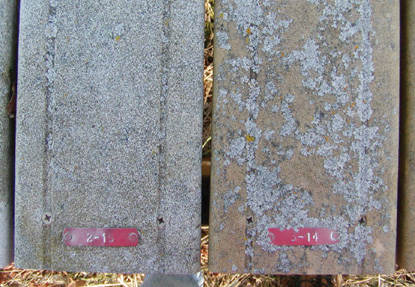
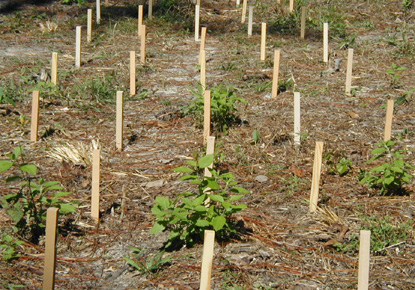
Mold and stain fungi
Fungi that grow superficially on wood are called molds, and those that cause discoloration of wood in storage and service are called stain fungi. Both mold and stain fungi are members of the Ascomycetes and Deuteromycetes (Fungi Imperfecti), yet a few of the molds are Zygomycetes (Mucorales). The aesthetic quality of wood-based products is significantly lowered as a result of discoloration by both mold and stain fungi. Stain fungi produce extracellular enzymes to utilize sugars, proteins, and extractives, which are nonstructural components of sapwood. In general, the stain fungi do not decay the structural components (that is, the wood cell wall), but some can cause soft rot. Mold and stain fungi are mainly an aesthetic problem for WPCs, but their effects are difficult to stop without periodic washing with dilute bleach solution.
Polymer degradation
WPCs exposed to weathering by solar radiation (ultraviolet light), oxidation, and rain water may experience color change as well as loss of mechanical properties. The color change affects the aesthetic quality, whereas the mechanical loss affects the performance. Weathering destroys the surface of the WPC by surface oxidation, matrix crystallinity changes, and interfacial degradation, which can lead to openings and pathways for moisture and decay to occur.
The UV resistance of WPCs is evaluated in the laboratory for minimum test durations of 2000 h of exposure in a weatherometer according to ASTM specifications. Flexural strength is determined before and after exposure. Various standards are used to reference both the plastic and the wood components. Mechanical and physical properties are determined, along with WPC degradation standards (that is, moisture, biodeterioration, UV resistance, and so on).
Methods of protection
As stated previously, fungi have four basic requirements (food, moisture, temperature, and oxygen). Temperature and oxygen are very difficult to control or limit, but moisture and nutrient exclusion can be regulated. Nutrient exclusion can be achieved by encapsulating the wood fibers in plastic, reducing the amount and size of wood in the WPC. It can also be achieved via the processing method. If the moisture content of the wood filler can be kept below 20%, then WPC decay may be prevented. This can be done not only by completely encapsulating the wood particles in plastic, but also by hydrophobation (treatments that increase water resistance) of the WPC surface or by chemical modification of the wood portion. The wood hydroxyl groups can be chemically modified to make them hydrophobic. This is done by either bulking the cell walls or cross-linking the cellulose hydroxyls. Chemical modification of the wood changes the wood fibers from hydrophilic to a permanent hydrophobic state. Anhydrides, isocyanates, and epoxides are the most common modification agents. Acetylation (bonding of an acetyl group onto an organic molecule) has been most actively investigated with solid wood because of its low toxicity and low cost, and it is currently being commercialized.
The most common way to protect WPCs from decay is via addition of additives such as chemical biocides or antimicrobials. The preservative zinc borate is often utilized because it has relatively low water solubility (making it resistant to leaching), it can withstand common extrusion temperatures, it has low toxicity (for both humans and the environment), and it has low cost. It is effective against wood decay fungi and insects, but it is not effective against mold and stain fungi at low concentrations. Other broad-spectrum treatments can be utilized against mold, mildew, and bacteria.
Photostabilizers are often added to WPCs to improve weatherability and decrease polymer degradation. For the polyolefins (plastics composed solely of carbon and hydrogen), ultraviolet absorbers (UVAs), free-radical scavengers, and pigments are generally used. Benzophenones and benzotriazoles are UVAs. Hindered amine light stabilizers (HALS) are an example of free-radical scavengers. Pigments are also utilized and protect by physically blocking the light. As an added bonus, they allow consumers to choose from a variety of colors for their product.
Moisture control is the key to protecting WPCs from biological decay and weathering, and to preserving ultimate performance. Research continues in this area with opportunities utilizing new and improved processing methods or new paints and surface coatings. Nanotechnology may also help with fundamental material characterization of the WPCs, and the use of nanoparticles may improve moisture, decay, and photodegradation resistance as well as thermal expansion and creep.
See also: Composite material; Lumber; Plastics processing; Polymer; Structural materials; Wood composites; Wood engineering design; Wood products; Wood properties