Key Concepts
A branch of engineering dealing with the design, development, and implementation of integrated systems of humans, machines, and information resources to provide products and services. Industrial engineering encompasses specialized knowledge and skills in the physical, social, engineering, and management sciences, such as human and cognitive sciences, computer systems and information technologies, manufacturing processes (see illustration), operations research, production, and automation. The industrial engineer integrates people into the design and development of systems, thus requiring an understanding of the physical, physiological, psychological, and other characteristics that govern and affect the performance of individuals and groups in working environments.
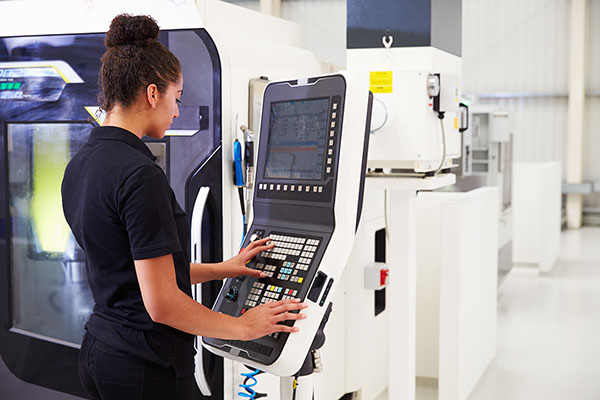
Functions and activities
Industrial engineering is a broad field compared to other engineering disciplines. The major activities of industrial engineering stem from manufacturing industries and include work methods analysis and improvement; work measurement and the establishment of standards; machine tool analysis and design; job and workplace design; plant layout and facility design; materials handling; cost reduction; production planning and scheduling; inventory control, maintenance, and replacement; statistical quality control; scheduling; assembly-line balancing, systems, and procedures; and overall productivity improvement. Computers and information systems have necessitated additional activities and functions, including computer numerically controlled (CNC) machines (see illustration) and programming; manufacturing systems design; computer-aided design/computer-aided manufacturing, design of experiments, quality engineering, and statistical process control; computer simulation, operations research, and management science methods; computer applications, software development, and information technology; human-factors engineering and ergonomics; systems design and integration; and robotics and automation.
The philosophy and motivation of the industrial engineering profession is to find the most efficient and effective methods, procedures, and processes for an operating system, and to seek continuous improvement. Thus, industrial engineering is utilized to help organizations grow and expand efficiently during periods of prosperity, and streamline costs and consolidate and reallocate resources during austere times. Industrial engineers, particularly those involved in manufacturing and related industries, work closely with management. Therefore, some understanding of organizational behavior, finance, management, and related business principles and practices is needed.
Functional areas
Industrial engineering can be classified into four areas: human factors and work systems, production and distribution systems, manufacturing systems, and operations research. This classification is in accordance with the various functions and activities in the design, development, and improvement of methods, operations, processes, and products.
Human factors and work systems
These combine the traditional areas of work measurement and design with the analysis and evaluation of the human element, which includes the physiological and psychological considerations in designing products and work systems. Technology continues to challenge the limitations and role of individuals and groups in production and service systems. Specifically, there is the challenge of matching capabilities such as the speed, touch, strength, and decision-making skills of humans with sophisticated computers and machine components. The influence and effects of noise, heat, humidity, lighting, and other environmental factors are dealt with in terms of the safety and welfare of the worker, as well as the evaluation of conditions for achieving optimum performance. Related issues deal with identifying and evaluating the information requirements and constraints associated with a system or design in order to achieve effective operation or service. See also: Control systems; Human-factors engineering; Human-machine systems; Facilities planning and design; Industrial health and safety; Methods engineering; Model theory; Optimization; Production systems; Productivity; Simulation; Systems analysis; Systems engineering; Work measurement; Work standardization
Production and distribution systems
These deal with the planning, scheduling, and flow of materials and information in production and manufacturing. This area includes the design, control, and implementation of production systems, including analysis procedures for determining where to locate people, machines, warehouses, and production centers; how to control and regulate the flow of parts and services to provide timely arrival of materials, acceptable quality, and customer satisfaction; scheduling and routing of operations; and maintenance and replacement procedures for ensuring cost effectiveness and overall productivity. See also: Inventory control; Materials handling; Production engineering; Production planning
Manufacturing systems
These consist of organized configurations of machines, workstations, information, and processes to transform materials into products, which include parts, assemblies, and subassemblies. The processes include machining, forming, assembly, inspection and testing, and transfer. They can be achieved through various levels of automation and hierarchical control. Design and development issues involve the specification and allocation of cells, buffer storage, computer integration, degree of automation, and inspection for overall effectiveness in producing high-quality, low-cost products to meet customer expectations. See also: Computer-aided design and manufacturing; Computer-integrated manufacturing; Flexible manufacturing system
Operations research
Operations research deals with the development and application of quantitative techniques and methods for analyzing and evaluating systems that aid in making engineering and management decisions. Management science, which is more often thought to be associated with business applications, is frequently used synonymously with operations research. This area includes the development and application of analytical, experimental, and simulation models for describing complex systems and prescribing conditions for efficient and optimal performance. Mathematical programming algorithms for allocating resources; methods for analyzing queueing and facility bottlenecking problems, inventory, and machine replacement decisions; and computer computation and implementation methods are among the issues dealt with in the field of operations research. See also: Artificial intelligence; Operations research; Queueing theory
Related subdisciplines
With its extensive breadth, industrial engineering has several subfields that overlap with neighboring disciplines, such as psychology, mechanical engineering, materials science, mathematics, computer science, business, and electrical engineering. Among the larger and more recognized subdisciplines are ergonomics, human factors, manufacturing engineering, operations research, operations management, statistics, and systems engineering. In many cases the extent of overlap is so significant, particularly in relation to research programs, that industrial engineering methodologies and techniques have been adopted and assimilated by other disciplines.
Industry 4.0
Industry 4.0, which is sometimes called the fourth industrial revolution, is the current and future age of smart factories, smart machines, and autonomous systems, which are driven by big data and analytics, autonomous and connected systems, and digital manufacturing (for example, 3D printing). Other important technologies of Industry 4.0 include the Internet of things, cloud computing, and cyber-physical systems controlled by machine-learning algorithms. See also: Algorithm; Artificial intelligence; Big data; Cloud computing; Internet of things; Machine learning; 3D printing