In the quest to manufacture and use building materials that are more environmentally friendly, soy adhesives can be an important component (Fig. 1). Trees fix and store carbon dioxide in the atmosphere. After the trees are harvested, machinery converts the wood into strands, which are then bonded together with adhesives to form strandboard, used in constructing long-lasting houses. Soybeans fix both carbon dioxide and nitrogen and can be converted into flour that can be made into a waterborne adhesive (glue) for bonding wood strands together. Although soy and other protein adhesives were used for centuries, fossil fuel–based adhesives have generally replaced biobased adhesives because they are more cost-effective and durable. However, new soy technology and an interest in low formaldehyde emissions for interior wood products are providing an impetus for a resurgence of biobased adhesives.
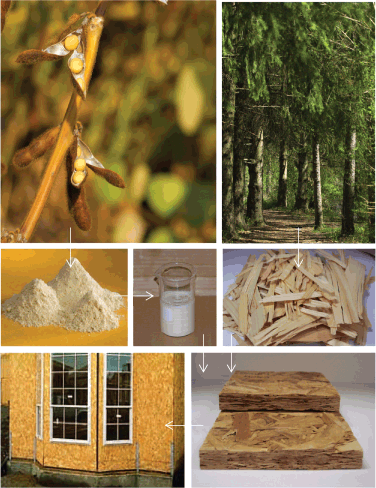
History
For millennia, humankind has used natural adhesives to make useful products. Since the early Egyptians used adhesives to bond wood veneer onto furniture, bonding wood has become common in applications from furniture assembly to roof beams. Traditionally, adhesives were based on proteins from animals (hoof, hide, blood, milk, and fish scales) and plants (soybeans). Among the wood products developed using protein adhesives were interior plywood (soybean adhesives) and glued laminated timber (glulam) beams (casein adhesives from milk). However, synthetic adhesives have generally displaced these protein adhesives.
Fossil fuel–based adhesives came into prominence in the twentieth century and have generally displaced biobased adhesives. Compared with many natural products, fossil fuels are relatively easy to convert into well-defined, uniform, specifically designed polymers. These synthetic polymers also provide greatly improved water resistance compared with standard biobased adhesives. Synthetic adhesives' resistance to heat, moisture, and decay helped to increase the wood product market for structural and exterior wood products. In recent years, however, volatile fossil fuel prices, a desire for renewable products, and the need to minimize formaldehyde emissions have led to opportunities for biobased adhesives—in particular, soybean-based ones.
Soybeans are an abundant agricultural crop with high oil and protein contents. The two main soy products are oil and meal. The oil is used for food and chemical applications, with alkyd (oil-based) paints being an example of the latter. Newer uses of the oil fraction are biodiesel fuel, and polyurethane and epoxide components. Soybean meal has mainly been used for animal feed and, to a limited extent, human food products. The meal ground into flour is the feedstock for making adhesives for wood bonding. The traditional method of dispersing the soy flour in water used aqueous caustic (sodium hydroxide). However, this type of adhesive had poor dispersion stability and poor water resistance after bonding.
Improved adhesives
To improve protein adhesives, it is important to realize that protein adhesives are different from other adhesives in two major ways. First, in chemical terms, most adhesives, whether synthetic or biobased, are polymers made from one or a few monomers, usually with similar functionality. However, proteins are made from more than 20 amino acid monomers with side chains containing a variety of functional groups. Second, morphologically, adhesives generally can be well described by understanding their primary and secondary structures. However, soy proteins also have tertiary and quaternary structures. Their polypeptide backbone not only influences the secondary structures of crystalline α-helix and β-sheet regions (which are distinct protein structural configurations), but also influences the specific folding that forms the tertiary structures. Understanding how conditions alter these tertiary structures is an active research area for fields ranging from enzymatic activity to prion (proteinaceous infectious particle)–related diseases. The protein folding influences polypeptide agglomerates, which is the quaternary structure.
Recent research on soy adhesives has focused on both dispersing and curing proteins. To form a satisfactory bond, soy flour with about 50% protein needs to be dispersed in water at high concentrations. Then, during the bonding process, the adhesive needs to be cured to provide water resistance for the bonded assembly.
The complex structure of soy proteins makes them more difficult to disperse or solubilize than most adhesives. Most soy proteins are complex polypeptide agglomerates referred to as the quaternary protein structure (Fig. 2). Breaking apart these agglomerates yields the individual polypeptides, still in their ball-shaped tertiary structure. Depending upon conditions, the ionic, hydrogen bond, disulfide, and hydrophobic associations holding the tertiary structure together may be opened to allow short- or long-range expansion, leaving the secondary structure of α-helices and β-sheets intact. Retention of some secondary structure is important to good adhesive performance. Dispersions tend to be unstable because proteins tend to associate with each other over time. These associations can have a dramatic effect upon viscosity, which is important for adhesive distribution and adhesion of the proteins.
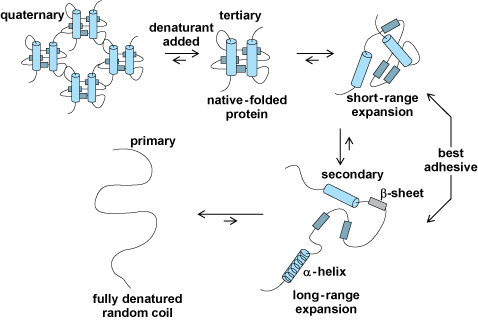
The curing process improves wet performance by decreasing the protein's water affinity and solubility. Given the variety of side-chain functional groups (amines, carboxylic acids, phenols, and thiols), many different chemicals can react with the proteins to cross-link the polypeptide chains. Research in recent years has focused on a variety of curing chemicals, including formaldehyde, phenol-formaldehyde, glutaraldehyde, and poly(amidoamine)-epoxy resin.
Currently, soy adhesives pass full exterior water exposure tests only when combined with fossil fuel–based adhesives. In such systems, soy proteins can lower the cost and improve the adhesives' performance, but the adhesives still depend upon a synthetic resin for the high moisture resistance. When soy is the main adhesive component, the resulting products are well suited for indoor applications. The absence of added formaldehyde with these adhesives eliminates the problem of urea-formaldehyde adhesives breaking down under hot and humid conditions.
Further opportunities for improving soy adhesives lie in increasing bond strength under wet conditions, increasing the protein concentration in the adhesive, and decreasing the cure time and temperature.
See also: Adhesive; Adhesive bonding; Formaldehyde; Polymer; Protein; Soybean; Structural materials; Wood composites; Wood engineering design; Wood products; Wood properties