Fueled by the demand for inexpensive garments with vibrant colors, Asia is leading the world in textile manufacturing. However, this textile manufacturing boom is having a significant environmental impact on the region. According to the World Bank, textile dyeing uses up to 200 tons of water per ton of fabric, and the resulting waste effluent is often discharged with a large amount of dye and other chemical pollutants. To reduce water use in textile dyeing as well as energy and chemicals, three companies—AirDye, Dyecoo, and SpinDye—have developed “waterless” dyeing processes and one company, ColorZen, has developed a near-zero-water dyeing process. See also: Asia; Dye; Dyeing; Textile; Textile chemistry; Water pollution
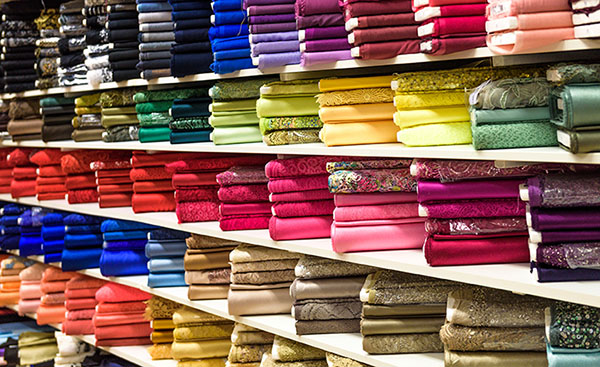
DyeCoo has developed waterless dyeing machines that use supercritical carbon dioxide as the solvent to dye polyester fibers and fabric, which comprise about 60 percent of the global garment market. The advantages of using DyeCoo's machines are that they use no water, produce zero wastewater (all the dye is used), reduce energy consumption by about 50 percent, and are 40 percent faster than traditional processes. Other than the dye, no additional chemicals are needed in the dyeing process, and the fabric comes out of the machines dry, which also saves energy by eliminating the need to dry wet fabric. DyeCoo states that their process brings production costs down by 30–50 percent. However, the investment cost of the machines—$2.5 to 4 million (U.S.)—is high. In addition, the process does not work on cotton fabric, which accounts for about 35 percent of the global garment market. See also: Carbon dioxide; Manufactured fiber; Polyester resins; Polymer; Supercritical fluid
ColorZen's process has been specifically designed for cotton dyeing. Traditional cotton-dyeing processes use large amounts of water, energy, and salt to fix the dyes on the fibers. Because salt is very hard and expensive to remove from the effluent, it is most often discharged along with 10–40 percent of the dye used in the process. ColorZen overcomes the need for salt by using a patented cationic (positively charged) pretreatment of the cotton fibers that improves attachment of anionic (negatively charged) dyes. ColorZen’s process is not waterless; however, it reduces water consumption by 90 percent. In addition, ColorZen’s technology dyes cotton in one-third the usual time, uses 75 percent less energy and 95 percent fewer chemicals, with zero toxic discharge. See also: Cotton; Natural fiber
Like DyeCoo, AirDye’s and SpinDye’s processes are waterless and applicable only to polyester. AirDye developed a printing process in which rolls of recyclable paper are coated with sublimable dyes that are transferred to fabric by a digitally driven thermal printhead. Variations in temperature control the amount of dye that sublimates, thus varying the color intensity. The dyes can be printed on the fabric as solids, patterns, or images. The printing machines use up to 86 percent less energy and produce 84 percent less greenhouse gas than traditional dyeing methods. SpinDye has taken the dyeing process, water, and chemicals out of the textile mills. It first melts recycled polyester and then adds the desired pigment colors. Next, it extrudes colored thread and spins it to produce yarn according to clients’ specifications. From there, the mills take the yarn and weave or knit it into fabrics. See also: Plastics processing; Recycling technology; Sublimation
All of these processes offer substantial environmental benefits, in terms of water use and pollution. At present, however, the processes are being used at just above pilot (small) scale for garments that are not too price-sensitive, such as sportswear. However, for mass-market acceptance and to be considered sustainable, the products will have to offer environmental benefits and be affordable for the manufacturer. See also: Green engineering