Key Concepts
A flexible, collaborative, and iterative process to provide the ability to manufacture quickly, effectively, and at minimal cost a component, assembly, product, or machine that meets particular operating specifications reliably and sustainably. Engineering design principles are basically the same whether the task is to design a small, simple object, such as a paper clip, or an immensely complicated machine or vehicle, such as a fighter aircraft able to execute a wide range of maneuvers in takeoff, landing, or in combat. The same basic principles apply whether a single engineer is involved with a simple design or multiple teams of engineers of different disciplines are working on different components, assemblies, and systems for a major project.
Process
The engineering design process can begin with a request or a need for a simple or complex physical object (see illustration) or system. For the process to get underway, several points must be defined: the intended function of the object or system; the size; the weight; the cost limitations; and the conditions under which it will function—including, for example, mechanical or environmental stresses. In the case of a complex machine or operating system, specifications for components and subsystems will have to be written and discussed within and among engineering teams, including the team with overall project responsibility, teams responsible for individual components and subsystems, as well as any teams responsible for maintaining ambient conditions such as temperature or humidity.
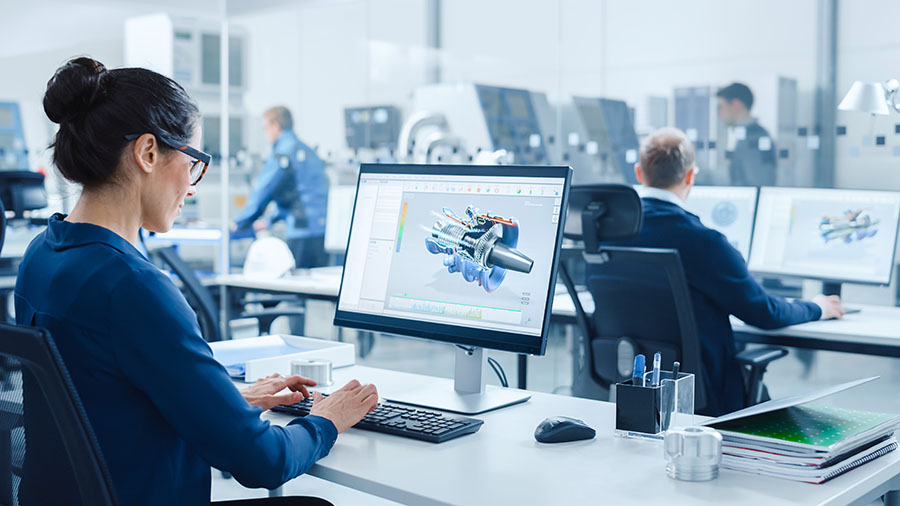
Consideration must be given to identifying the engineering specialties that a particular project requires. Take, for example, planning for an automated warehouse. Systems for materials handling and accounting require a sophisticated level of specifications in response to multiple questions: How large will the warehouse be? How many different items will it contain? How varied will they be in shape, size, and weight? How many orders will need to be fulfilled in a day? Construction engineers, working with warehouse management, will have to construct a warehouse of appropriate size. Systems and software engineers will have to specify and develop software that can operate warehouse distribution and accounting systems. Mechanical and industrial engineers will have to design, order, and install machinery (conveyor belts, forklifts, etc.) that can move items to stations where they can be packaged, labeled for shipping, and loaded onto trucks. See also: Construction engineering; Facilities planning and design; Industrial engineering; Materials handling; Mechanical engineering; Software engineering; Systems engineering
Research
Research is a key activity in the engineering design process. Engineers may need, for example, to learn about and discuss any environmental effects a vehicle or structure might be subjected to and how to ameliorate those effects. Methods for mitigating environmental degradation of materials, such as discoloration and rust, might have to be studied. Experts in the application of protective coatings might have to be added to the engineering team.
Materials
Materials selection is another important activity. Analytical methods, such as the use of performance indices, can help engineers determine trade-offs in strength, durability, weight, and cost so that materials appropriate for particular situations can be specified. Engineering design has benefited from technological advances that have led to the development of novel materials to replace heavier, less durable, and more expensive traditional materials. See also: Materials science and engineering
Codes and standards
Knowledge of codes and standards can be critical in engineering design. There are, for example, boiler, pressure vessel, and piping codes that govern design, construction, and operation of such equipment so that ruptures do not occur and cause destruction and injury. Engineering societies, such as the American Society of Mechanical Engineers, have developed many such codes. There are many electrical codes developed by electrical and electronics engineering societies that must be followed. Standards can come into play in many ways: To take several examples, government-mandated energy efficiency and fuel efficiency standards exist for household appliances and automotive vehicles; manufacturing or chemical plants should be designed so they meet legal air or water pollution requirements. Another way standards can come into play is when parts are sourced from suppliers worldwide, and engineers must be able to trust and verify that the parts meet identical functional specifications, no matter their origin.
Strength of materials
Analysis related to the strength of materials to be used in an assembly or machine is another key activity. Engineers need to determine, for example, the stress levels that individual components will be subjected to when a machine is operating. Such analysis begins when engineers activate their computer-aided design (CAD) workstations. CAD systems began to replace pencil-and-paper drawings in the 1960s and are now ubiquitous in numerous industries. Different versions of CAD systems are used in different engineering disciplines. Drawings of components, entire structures, or machines in two and three dimensions help engineers conceptualize various versions of what they are designing and enable them to employ techniques for stress and dynamic calculations so that the engineers can analyze the viability of those components. These calculations and analyses will show whether design changes are required. Should some components be increased in size so they can better withstand stresses? Should some material specifications be reconsidered? CAD systems also produce electronic files that are used for manufacturing operations, as well as for documentation, such as bills of materials and drawings that enable engineers to track revisions to designs. See also: Computer-aided design and manufacturing; Strength of materials
Design for manufacturing and assembly
Design for manufacturing and assembly (DfMA) is an engineering design approach that focuses on ease of manufacturing and efficiency of assembly. DfMA deals with selecting cost-effective materials and production techniques for particular applications and with reducing the complexity of manufacturing and assembly operations, by, whenever possible, reducing the number of such operations. DfMA is particularly important in reducing costs and speeding production lines in the manufacturing of high-volume, complex consumer goods, such as appliances and automobiles. DfMA also enables engineers to source components, subassemblies, and even some manufacturing operations from suppliers worldwide, thereby reducing cost.
Green design
Other variations to a standard engineering design approach involve green design. These variations include design for environment, which considers environmental, health, and safety aspects of a design over a product’s lifetime; product design for sustainability, which involves maintaining the environment over the operating life and disposal or reuse of a product; life-cycle design, which is a means of improving the environment through product design; design for reliability, which is an important benefit for planning, design, and operation of systems and machines; design for maintainability, which involves ease and cost of continued and corrective maintenance; and design for remanufacturing processes, which involves making a nonfunctioning or retired product like new through a series of industrial operations. See also: Green engineering; Product design; Reliability, availability, and maintainability; Sustainability
Testing
An important, again iterative step in the engineering design process involves testing a design. In some circumstances, a design prototype, or model, can be built and tested. Test results can be analyzed to determine how efficiently a system or machine will operate and to determine whether any adjustments need to be made to a design. When an entire operating system run by software, or a piece of machinery, such as an automobile or an aircraft, has been constructed based on an engineering design, it should then be subjected to rigorous tests. Before a software-driven operating system is activated or production lines are started up, engineers need to be confident that whatever they have designed can withstand stresses that will be encountered during operation under adverse conditions. A warehouse operating system, for example, should be tested under heavy order volumes. A newly designed automobile should be tested on a proving ground that is difficult to navigate. A newly designed aircraft should be put through its paces by skilled test pilots. See also: Aircraft design; Prototype
Making changes to a design so that a system or machine can successfully pass rigorous stress tests should not lead to a conclusion that a design, even after required adjustments, is flawless and need never be changed. Performance of an original system or machine, or of products that roll off an assembly line, should be monitored over time and under continually varied ambient and environmental conditions so as to determine whether the adjusted design still has hidden inherent flaws.
End of life
Finally, engineering design should consider what to do with systems, products, and machines when their useful life has ended, when they cannot be remanufactured, or when not all of their components can be repurposed. They should be designed so that they can be disposed of in an environmentally conscious way.