Key Concepts
A vehicle that uses two or more sources of energy for propulsion. Typically, one source of energy is a liquid or gaseous fuel, and the other is an energy-storage system such as a battery or ultracapacitor. Other options for energy storage include compressed gas, pressurized liquids (hydraulics), and mechanical energy stored in a flywheel. The most common type of hybrid vehicle is the hybrid electric vehicle (HEV; Fig. 1), which typically uses a liquid fuel (gasoline, diesel, or a gasoline/ethanol blend) to power an internal combustion engine that works with batteries, or ultracapacitors, to power an electric motor. See also: Alternative fuels for vehicles; Battery; Diesel fuel; Energy storage; Flywheel; Gasoline; Internal combustion engine
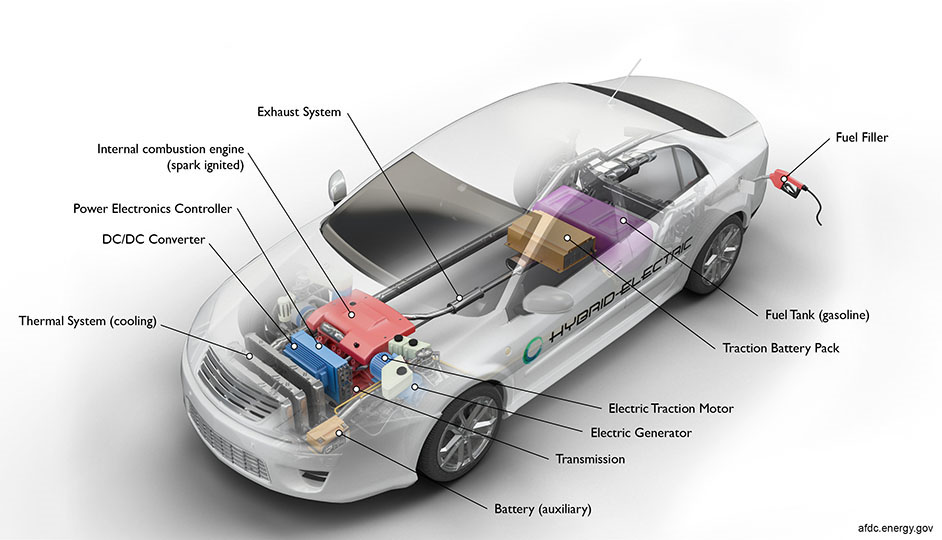
Why use hybrid vehicles?
Technology in automobiles has progressed significantly since their introduction around the beginning of the twentieth century. At the same time, increasing urbanization is exposing drivers to greater amounts of efficiency-reducing congestion and the associated increases in harmful air pollution resulting from combustion. Consequently, it is useful to consider alternative means of personal and commercial transportation in which fuel use and pollution are less affected by urban driving conditions. HEVs are one such alternative technology that can use less fuel and pollute less in urban driving, while maintaining performance levels comparable to current conventional vehicles. Of the alternative powertrain (mechanical components that drive the wheels) options, HEVs appear to be among the best choices for providing near-term reductions in oil use (and corresponding cost) and air pollution, as evidenced by their increasing commercial availability from many manufacturers. See also: Air pollution; Combustion
Efficiently satisfy the vehicle driving forces
In physics, energy is defined by the force exerted over a distance. For vehicle energy use, four forces dominate. Newton's second law of motion is shown in the equation F=ma, where F is the force required for a specified mass m to be accelerated at a rate of a. As suggested here, the force (and hence, the fueling rate) required to move a vehicle increases for heavier vehicles and for frequent rapid vehicle speed changes (which create large accelerations). Much of the energy used to accelerate a vehicle is then stored as kinetic or motion energy, which is equal to ½mv2, where v is the velocity of the vehicle. Conventional vehicles waste nearly all of that kinetic energy by dissipating it as thermal energy with friction brakes. HEVs, on the other hand, recover that kinetic energy through regenerative braking. That is, the wheels turn the shaft of an electric motor to generate electricity, which is then stored in the batteries (or other electrical energy storage device). However, the power generated by braking can be much higher than the power rating of the motor and batteries. Consider that the kinetic energy of a midsized vehicle weighing 1500 kg (3360 lb) traveling at 120 km/h (75 mi/h) is about 833 kJ. A braking event of 8 s to stop the vehicle would produce more than 100 kW of power, which is higher than the recharge rate that many systems could accept. See also: Brake; Energy; Newton's laws of motion
The additional force a vehicle must overcome when it climbs a hill is F = mg sin(θ), where g is the gravitational constant and θ is the angle between the horizontal and the road surface. Although force is required to climb a hill, the vehicle's potential energy increases with increasing elevation. When a conventional vehicle descends a steep hill, the mechanical brakes again convert potential energy to waste heat energy to maintain the vehicle at a safe speed. However, an HEV descending the same hill benefits from the ability to convert potential energy and store it as electricity through the regenerative braking process.
Vehicles also face an opposing force to push through the surrounding air. This is known as aerodynamic drag and is equal to ½ρCdAfv2, where ρ is the density of air, Cd is the coefficient of drag for that vehicle's design (including the effects of vehicle shape, wheel wells, underbody, etc.), and Af is the frontal area of the vehicle. This equation again illustrates that vehicle design and use (for example, high-speed driving) affect the force and, hence, the fuel required to operate the vehicle. Design improvements to minimize aerodynamic drag can be applied to any vehicle platform, but they occur with greater frequency in HEVs because such improvements emphasize efficiency. Typical drag coefficients are 0.40–0.45 for light trucks and 0.30–0.35 for cars. For example, the drag coefficient for the Toyota Prius HEV is 0.26, and the Honda Insight HEV drag coefficient is 0.25. In comparison, an F-16 Fighting Falcon jet has a Cd of 0.0175. These lower drag coefficients in HEVs ensure that a significant amount of the force that accelerates the vehicle goes into recoverable kinetic energy rather than dissipation to aerodynamic drag. See also: Aerodynamics
The last significant force is overcoming the rolling resistance of the vehicle, which is equal to Crrmg, where Crr is the coefficient of rolling resistance for the tires, m is the vehicle mass, and g is the gravitational constant. As with drag reductions, efforts to reduce tire rolling resistance are not unique to HEVs, but may be included in those vehicles as part of the overall fuel-saving package. Rolling resistance for car tires on a hard, paved surface is 0.007–0.013. For comparison, train wheels on steel have a rolling resistance of less than 0.0025. See also: Tire
Efficiently convert fuel to motion energy
A conventional vehicle ultimately derives all of the energy to satisfy the vehicle’s driving requirements from its liquid fuel. The same is true of a standard HEV, except that electric components can help the engine use fuel more efficiently. The engine size in a conventional vehicle is typically dictated by the largest expected power requirement over a brief duration, such as that to satisfy a 0–97 km/h (0–60 mi/h) acceleration in 8 s. During other driving situations, the vehicle power is often quite a bit lower than this peak value (power is calculated by multiplying vehicle speed by the sum of the force equations). Engines are most efficient when operated at substantial power levels, and efficiency drops off significantly at low power levels (see the conventional engine efficiency curve in Fig. 2). This creates the counterintuitive phenomenon of vehicles often achieving better fuel economy while cruising at speeds of 65–75 km/h (40–47 mi/h) than at 25–35 km/h (16–22 mi/h). Even though the road load power demands increase with increasing speed, the increase in engine efficiency more than compensates for it by moving up the steep portion of the efficiency curve (Fig. 2). See also: Power
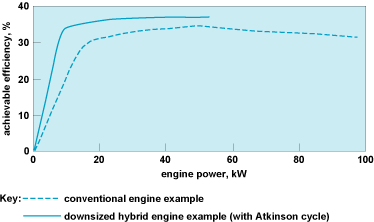
In a comparable HEV, the engine can be smaller because the electric motor assists the engine during momentary peak power events. Compared with a larger engine, a downsized engine shifts to lower power levels in the lower efficiency region of operation (Fig. 2). This means that a smaller engine will use less fuel to satisfy the significant amount of vehicle operation that requires relatively low engine power output. Also, for very low power levels, an HEV engine might turn off altogether and allow the electric motor to propel the vehicle. At slightly higher but still fairly inefficient power levels, the engine might be used to power the vehicle's wheels and to turn the shaft of the electric motor, generating electricity to store in the batteries. The added load of the motor on the engine requires additional fuel, but it helps the engine operate at a higher efficiency and stores electrical energy that the motor can use later to help propel the vehicle. This process is known as “load leveling” the engine. The added control capability provided by the electric drive components can enable an HEV to use engine technologies with higher peak efficiencies but a narrower operating range than those typically employed in conventional vehicles. This is the case with the Atkinson cycle engines used in the Toyota Prius and Hyundai Ioniq, for example. Importantly, HEVs can achieve similar peak accelerations because the motor can supplement the power of the engine during brief, hard accelerations. See also: Motor
Efficiently power the vehicle's ancillary loads
A conventional vehicle engine continues to burn fuel even when the vehicle is idling and requires no power for propulsion. This keeps the engine operating so that it can provide power as soon as the driver accelerates and keeps powering the vehicle's ancillary loads, which run off belts attached to the engine crankshaft. Ancillary power is required for low-voltage electronics, such as lighting and entertainment systems, power steering and power braking assistance, and climate control (up to 6 kW during cabin cool-down). In an HEV, these ancillary loads can be electrified, which alleviates their drag on the engine and allows them to operate more efficiently (rather than being tied to the speed of the engine). HEVs can therefore turn off rather than idle their engines when stopped and rely on their batteries to power the required ancillary loads. Because an electric motor, unlike an engine, can provide near-full torque before it begins to spin, the electric motor can then launch the vehicle and restart the engine after the vehicle is in motion. See also: Automotive brake; Automotive steering
Summary of efficiency improvements
Hybrid vehicle designs will include some or all of the following: regenerative braking to recapture kinetic and potential energy; a downsized engine that uses electric motors to assist with acceleration; electric launch and low-speed electric-only operation; load-leveling of the engine for efficient operation and battery charging; advanced engine technologies; an engine that turns off at idle; and efficient electric accessories.
In addition to these hybrid functions, HEVs can benefit from efficiency improvements that could be applied to any vehicle. These include reducing vehicle mass (such as through use of lightweight materials), lessening aerodynamic drag, and lowering rolling resistance. Design changes to reduce ancillary loads can improve the efficiency of any vehicle but are particularly important for HEVs, as high loads can increase the fuel consumption of an energy-efficient vehicle by as much as 50%. Similarly, less aggressive driving (such as avoiding rapid speed changes and excessive speeds) can improve the efficiency of any vehicle and make a particularly large impact on an HEV. Other areas of research into broadly applicable vehicle component improvements include work on advanced combustion and variable compression ratio engines and transmissions with high numbers of gears or with continuously variable effective gear ratios. See also: Automotive transmission; Compression ratio; Gear
Hybrid electric vehicle components
HEVs add three major components to conventional vehicle designs: energy storage, electric motors, and power electronics.
Energy storage system/batteries
Typically, lithium-ion batteries with liquid electrolytes are used in HEVs, although automakers are considering solid-state lithium-ion batteries for future use. The challenge is to develop low-cost batteries with high energy density (for extended use), high power density (for short bursts of high power to accelerate and accept high rates of regenerative energy), and long life that are safe for consumer use. A key issue is the state-of-charge window—that is, how much of the available energy can be used without significantly degrading the life of the battery. Ambient low and high temperatures affect battery life and performance. In addition, charging and discharging the battery generate heat that must be managed.
Electric motors and generators
Electric motors can convert electrical energy from the batteries into mechanical energy to help drive the wheels of the vehicle. An electric motor can typically also operate in reverse as a generator, taking mechanical energy to drive its shaft and creating electrical energy, such as during regenerative braking. Typically, three-phase alternating-current (ac) motors (also known as brushless dc motors) are used because of their cost, efficiency, and reliability. See also: Alternating current; Direct current; Generator
Power electronics
The electronics required for HEV operation include an inverter to switch between ac power for the motor and direct-current (dc) power for the energy storage systems, as well as converters to change the voltage of the battery system to a lower voltage for ancillary devices or to a higher voltage for more efficient motor operation. A 100-kW inverter operating at 95% efficiency generates 5 kW of heat that must be managed to ensure long component life.
Hybrid powertrain designs
Different HEV design approaches are possible with different component arrangements. The two classic HEV designs are known as “series” and “parallel” configurations (Fig. 3). A series configuration has no direct mechanical connection between the engine and the vehicle wheels. The engine is used simply to power a generator, which provides electricity that is used by an electric motor to drive the wheels or is stored in the vehicle's batteries for later use. This configuration enables precise control of the engine near its point of highest efficiency. However, the electric drive components for a series vehicle must be very large to satisfy peak driving demands. The Chevy Volt plug-in hybrid has a more complicated powertrain than the classic series HEV design; but, over much of its operation, it will behave as a series configuration. Plug-in hybrid vehicles are discussed in the final section of this article.
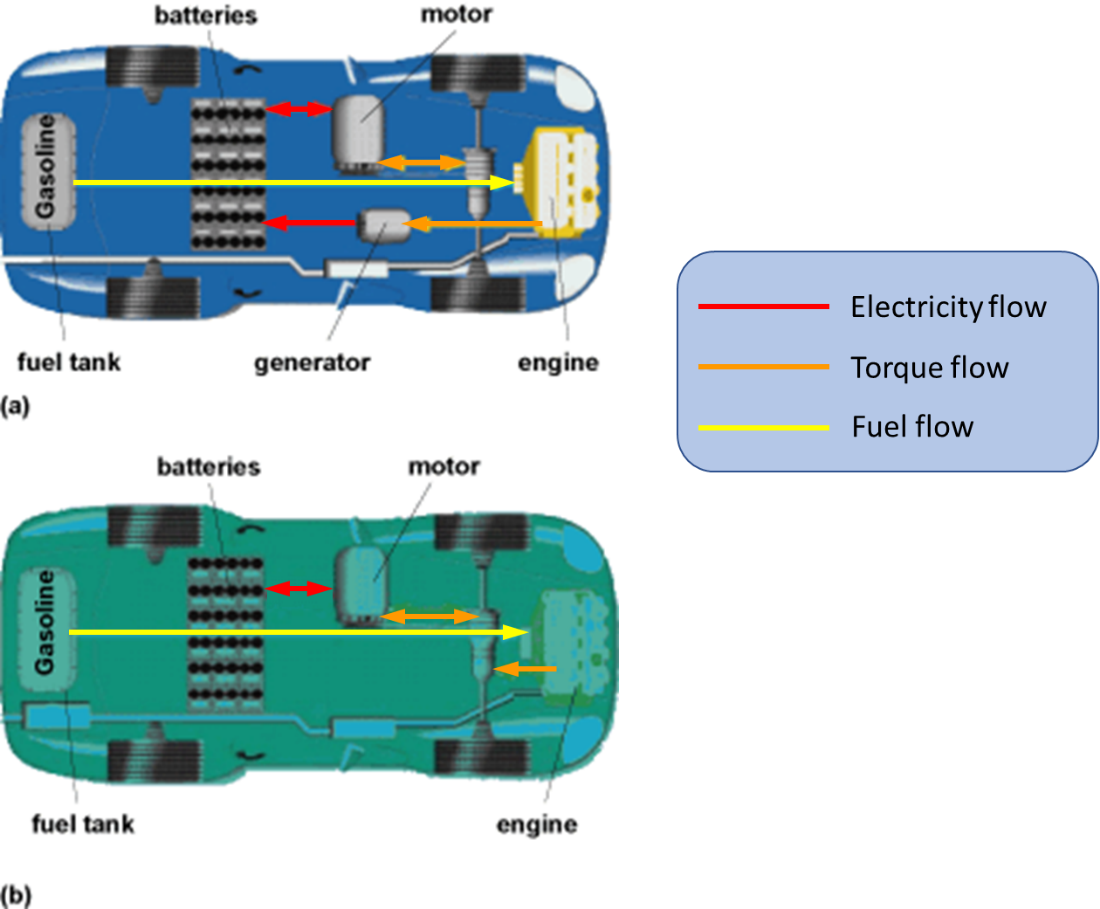
One disadvantage of a series configuration is the inefficiency associated with taking mechanical energy from the engine crankshaft, converting that mechanical energy into electrical energy with the generator, and then converting electrical energy back to mechanical energy with the electric motor to turn the driveshaft. In a parallel configuration, the engine can directly power the wheels; and the electric motor works in parallel to provide or absorb supplemental power. Mechanically connecting the engine directly to the wheels avoids the double-conversion loss of the series configuration but makes it more difficult to operate the engine at peak efficiency. Several commercial HEVs use more complicated variations of the classic design configurations to take better advantage of the benefits of each, including the power-split approach used in the Toyota and Ford HEVs and the two-mode (involving multiple clutches) configuration used in the Hyundai Ioniq hybrid.
HEVs are often discussed with respect to their approximate placement on a continuum (low to high) from “micro” and “mild” to “full” hybrid. In general, hybrids moving up the spectrum use larger batteries and higher power motors (relative to the size of the vehicle's engine) and take advantage of more of the hybrid functions discussed previously. Hybrids on the lower end of the spectrum may also have their electric motors directly coupled to the engine, whereas those on the upper end can generally operate the drivetrain with the electric motor alone. Many vehicles can now be classified as micro-hybrids. The Ford F-150, for example, can be classified as a micro-hybrid because this vehicle features a stop/start capability in which the engine captures a small amount of regenerative energy during braking, is turned off when the vehicle is stopped, and is restarted when the vehicle needs to move again. A system like this typically provides no assistance with propulsion, which is handled entirely by the engine. The Toyota Prius, on the other hand, is classified as a full hybrid because it has larger electrical components (battery, motors, etc.) that operate at higher voltage, capture more regenerative energy, and significantly assist with propulsion. These vehicles follow the trend of increasing relative electric component size and increasing number of hybrid functions, beginning with engine start/stop capability up to full electrical operation and extensive engine load-leveling capability.
Do HEVs save fuel?
Toyota alone sold more than 250,000 HEVs in the United States in 2019. More than one hundred HEV models are currently available to consumers. Fuel consumption is reduced by almost 50% for some vehicles in city driving (see Table), where significant kinetic energy is recaptured, the engine shuts off during idling, and the electric motor assists with acceleration. Fewer benefits are realized at relatively constant highway speeds.
City label, mpg | Highway (HW) label, mpg | Combined label, mpg | HEV fuel reduction, % | |||||||
---|---|---|---|---|---|---|---|---|---|---|
Hybrid electric vehicle (HEV) | Standard (Std.) vehicle | HEV | Std. | HEV | Std. | HEV | Std. | City label | HW label | Combined |
Hyundai Ioniq | Hyundai Elantra 1.4L | 55 | 33 | 54 | 41 | 55 | 36 | 40 | 24 | 35 |
Toyota Corolla Hybrid | Toyota Corolla 2.0L | 53 | 32 | 52 | 41 | 52 | 35 | 40 | 21 | 33 |
Honda Insight | Honda Civic 1.5L | 55 | 32 | 49 | 42 | 52 | 36 | 41 | 14 | 31 |
Toyota Camry Hybrid | Toyota Camry | 51 | 29 | 53 | 41 | 52 | 34 | 43 | 23 | 35 |
Honda Accord Hybrid | Honda Accord 1.5L | 48 | 30 | 48 | 38 | 48 | 33 | 38 | 21 | 31 |
2019 Chevrolet Malibu Hybrid | 2019 Chevrolet Malibu 1.5L | 49 | 29 | 43 | 36 | 46 | 32 | 41 | 16 | 30 |
Lexus ES 300h Hybrid | Lexus ES 350 3.5L | 43 | 22 | 44 | 32 | 44 | 26 | 49 | 27 | 41 |
Ford Fusion Hybrid | Ford Fusion 1.5L | 43 | 23 | 41 | 34 | 42 | 27 | 47 | 17 | 36 |
Toyota Highlander Hybrid AWD | Toyota Highlander 3.5L AWD | 35 | 20 | 35 | 27 | 35 | 23 | 43 | 23 | 34 |
2019 Nissan Rogue Hybrid AWD | Nissan Rogue 2.5L AWD | 31 | 25 | 34 | 32 | 33 | 27 | 19 | 6 | 18 |
Ford Explorer Hybrid RWD | Ford Explorer 2.3L RWD | 27 | 21 | 29 | 28 | 28 | 24 | 22 | 3 | 14 |
What are the barriers?
The most significant barrier to wider acceptance of HEVs is the additional cost for batteries, power electronics, and electric motors. These components also add packaging and assembly challenges.
Plug-in HEVs, fuel-cell vehicles, and electric vehicles
Hybrid vehicle technology is not an entirely new concept. Hybrid and electric vehicles (EVs) were available in the late 1800s and early 1900s. The abundance of oil supplies at that time eventually contributed to conventional combustion-engine vehicles winning out as the dominant vehicle technology during the twentieth century. More recently, growing concern about the continued availability of petroleum reserves and greenhouse gases emitted from burning fossil fuels has led to renewed interest in hybrid and other alternative powertrain technologies.
Plug-in hybrid electric vehicles (PHEVs) are HEVs that include a charging plug and sufficient energy storage so the vehicle can be charged from an electrical outlet to cover much, if not all, typical daily driving. PHEVs have all the benefits of HEVs and can operate from domestically produced electricity, which provides increased fuel reliability from greater fuel diversification. Two major designs are being considered today. One provides true all-electric driving that can operate solely by the electric powertrain. The Chevrolet Volt is this kind of PHEV, which requires that the battery pack, electric motors, and power electronics be sized for all vehicle operation. The other design, called a blended control strategy, uses the electric powertrain for much of the driving but depends on an engine for rapid (high-power) acceleration. The Hyundai Ioniq represents this kind of PHEV. By foregoing all-electric operation over a full range of driving conditions, the blended design can use smaller battery packs, motors, and electronics. In either case, the battery pack energy may be sized to displace fuel use for some distance—for example, 16–64 km (10–40 mi) of conventional HEV operation. Increased use of PHEVs would have a substantial impact on oil consumption because the average vehicle trip length is about 16 km (10 mi), and daily travel distances per driver average less than 48 km (30 mi). PHEVs can substantially reduce our dependence on oil, provide more reliable personal transportation, use renewable energy to provide battery charging, and shift air pollution from urban centers during rush hour to more remote locations during nighttime vehicle charging. A battery pack that provides 64 km (40 mi) or less of driving range can be recharged overnight from a conventional 110- to 120-V outlet. A key benefit of PHEVs relative to an all-electric vehicle is that the vehicle need not carry a large battery pack, which is only fully used for longer but less-frequent trips. PHEVs can travel hundreds of miles on a single tank of gas but are able to accomplish most daily driving tasks purely on battery power. See also: Electric vehicle
Fuel-cell vehicles (FCVs) are already being demonstrated, but they must overcome several barriers before mass introduction. The required improvements include a lower cost fuel-cell stack, increased robustness in a range of weather conditions, more effective onboard hydrogen storage, and an efficient hydrogen production and distribution infrastructure. To reduce the size and cost of the fuel-cell stack and to take advantage of regenerative braking, FCVs will also be HEVs (or even PHEVs). See also: Fuel cell
The simple design of electric vehicles (EVs) has many benefits. Many EVs have been built and demonstrated. Current challenges include the high cost of the energy storage system, the need for more high-voltage charging stations, development of safer battery packs with higher energy densities, and the time to efficiently charge the batteries.
Advances in HEV technology (such as energy storage, electric motors, power electronics, and control strategies) will benefit PHEVs, FCVs, and EVs as those vehicles become near-term options.