Key Concepts
Power derived from fission nuclear reactions. Conventionally, nuclear power is interpreted as the utilization of the fission reactions in a nuclear power reactor (Fig. 1) to produce steam for electric power production, for ship propulsion, or for process heat. Fission reactions involve breaking up the nucleus of high-mass atoms and yield an energy release which is more than a millionfold greater than that obtained from chemical reactions involving the burning of a fuel. Successful control of the nuclear fission reactions utilizes this intensive source of energy. See also: Atom; Atomic nucleus; Atomic physics; Electric power generation; Electricity; Heat; Nuclear fission; Nuclear reaction; Nuclear reactor; Ship nuclear propulsion
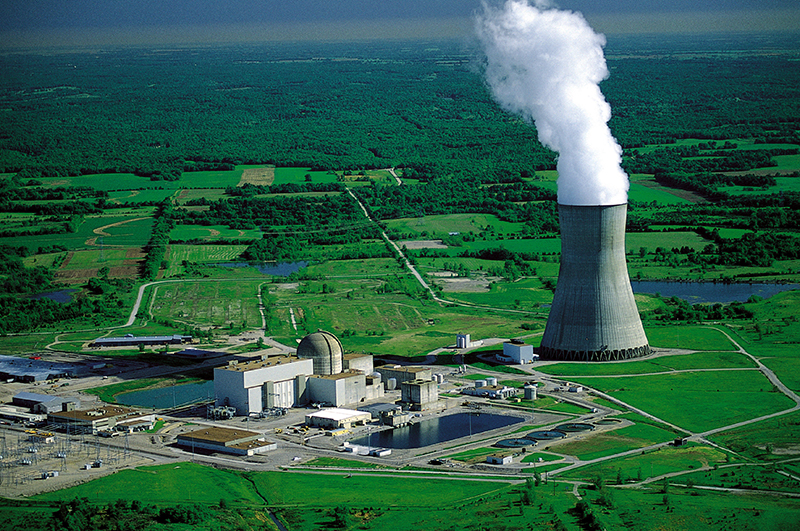
Fission reactions provide intensive sources of energy. For example, the fissioning of an atom of uranium yields about 200 MeV (megaelectronvolts), whereas the oxidation of an atom of carbon releases only 4 eV (electronvolts). On a weight basis, this 50,000,000:1 energy ratio becomes about 2,500,000:1. Natural uranium consists of several isotopes, only 0.7% of which is uranium-235, the fissile fuel used in reactors today. Even with these considerations, including the need to enrich the fuel to several percent uranium-235, fission reactions are attractive energy sources when coupled with abundant and relatively cheap uranium ore. See also: Electronvolt; Energy; Oxidation-reduction; Uranium
At some point in the future, “nuclear power” could also include electricity generation from nuclear fusion, the reaction that powers the stars. Decades of development of nuclear fusion capabilities, however, have not yet succeeded in producing sustained, controlled, net-positive energy production, due in large part to the many difficulties inherent in the necessity to maintain a plasma under Earth conditions at temperatures of approximately 100 million °C (180 million °F). See also: ITER (International Tokamak Experimental Reactor); Harnessing the power of nuclear fusion in tokamak reactors; Nuclear fusion; Plasma (physics); Star; Sun
Power reactor types
The first nuclear reactor designs were developed in the 1940s for military purposes. The first prototypes for civil nuclear reactors followed in the 1950s. Since that time, four generations of nuclear power systems have been recognized. See also: Nuclear reactor
Generation I
The prototypes and earliest commercial nuclear power plants brought online in the 1950s and 1960s comprise the first generation. Notable stations and reactor types include the first grid-connected commercial reactor at the Obninsk Nuclear Power Plant in the former Soviet Union in 1954, which operated until 2002; the first pressurized-water reactor at the Shippingport Atomic Power Station in Pennsylvania, which ran from 1957 to 1982; the first boiling-water reactor at the Dresden Generating Station in Illinois, from 1959 to 1978, and the last Generation I plant, the Wylfa Nuclear Power Station in Wales, which shuttered in 2015 after operating since 1971.
Generation II
Globally, the vast majority of the approximately 450 reactors currently in commercial operation, as well as those that have been decommissioned and the more than 50 new reactors under construction, are light-water-moderated and -cooled reactors (LWRs) known as Generation II reactors. This reactor type is further broken down into the pressurized-water reactor (PWR) and the boiling-water reactor (BWR), with the former accounting for about two-thirds of all reactors in service. A variant, the pressurized heavy-water reactor (PHWR), represents just over 10% of the worldwide reactor census and is used primarily in Canada and India. The United Kingdom uses another reactor type, called a gas-cooled reactor.
Of these concepts, the water-cooled and gas-cooled reactors are thermal reactors; that is, they operate by using moderated neutrons slowed down to “thermal” velocities (so called because their speed is determined by the thermal, or kinetic, energy of the substance in which the fuel is placed, namely, the moderator). A third type, the fast-neutron reactor, operates on unmoderated neutrons that have high velocities near to those with which they are released from a fissioning nucleus. See also: Neutron; Thermal neutrons
Generation II reactors are typically designed for 40-year lifetimes, have active safety mechanisms (that is, requiring electrical or mechanical operation), and use enriched uranium fuel.
Pressurized-water reactor (PWR)
In PWRs, water flows through the reactor core in a coolant loop, reaching temperatures of about 325°C (617°F). A pressurizer is used in the primary system to maintain about 150 atm (15 MPa) pressure to suppress boiling in the primary coolant. The pressurized water in the coolant loop runs to a steam generator, where the heat vaporizes water kept in a lower-pressure secondary loop. A steam line sends the generated vapor to drive a turbine, producing electricity. PWRs typically have 150–250 fuel assemblies and utilize 80–100 metric tons of uranium as nuclear fuel.
Boiling-water reactor (BWR)
In contrast to PWRs, though the reactor types are very similar, BWRs have a single circuit through which water moves. Some of the water is intended to boil as it absorbs heat from the core, and so the water is kept at a lower atmospheric pressure of about 75 atm (7.5 MPa), lowering its boiling point to 285°C (545°F). A liquid–steam mixture exiting the top of the core moves through steam separators, removing droplets and leaving steam that is directed via a steam line to drive a turbine. A BWR core may contain up to 750 fuel assemblies utilizing about 140 metric tons of uranium.
Generation III
The so-called advanced light-water reactors (ALWR) that comprise Generation III power reactors evolved from operating experience with light-water reactors. Generation III reactor types offer higher reliability, have fewer components and complex systems, and are easier to build and maintain. They also offer a higher degree of safety by the use of redundant, passive systems that do not require power for actuation. Low sensitivity to transients is achieved through low power density in the reactor core and a large inventory of coolant and containment water.
The first advanced nuclear plant to be constructed was a twin-unit advanced boiling-water reactor (ABWR; Fig. 2) at the Kashiwazaki-Kariwa site in Japan, which produced power for the electric grid starting in 1996, 58 months after groundbreaking. In 1998, following a 12-year design program, the AP-600 plant became the first advanced light-water reactor to be certified by the U.S. Nuclear Regulatory Commission.
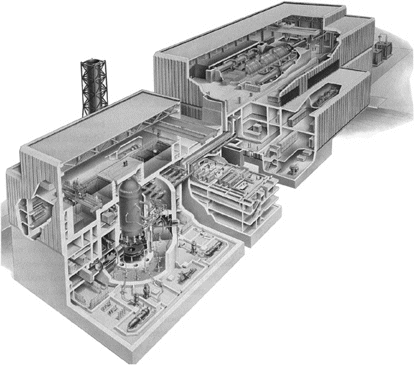
Generation IV
The next generation of power reactors is not expected to enter service until the 2030s or 2040s. Generation IV reactors are being designed to use novel architectures and potentially fuels such as thorium. Reactors could also come in smaller sizes than legacy systems. Some Generation IV concepts envision more complete utilization of the radioactive fuel source, reducing or even eliminating radioactive waste and closing fuel cycles. Fast reactor types being studied include gas-, lead-, and sodium-cooled reactors, along with thermal reactor types such as very-high-temperature, molten-salt, and supercritical-water–cooled varieties.
Nuclear fuel cycle
Although the main process of nuclear power is the release of energy in the fission process that occurs in the reactor, a number of other important processes, such as mining and waste disposal, both precede and follow fission. Together they constitute the nuclear fuel cycle. See also: Nuclear fuel cycle
The only fissile material found in practical abundance in nature is uranium-235. Plutonium becomes part of the fuel cycle when the fertile material uranium-238 is converted into fissile plutonium-239. Thus, the dominant fuel cycle is the uranium–plutonium cycle. If thorium-232 is used in a reactor to produce fissile uranium-233, another cycle occurs, the thorium–uranium cycle. Because applications of the latter have been limited to small-scale tests and a commercial thorium–uranium cycle has not been developed, the following discussion concentrates on the uranium–plutonium cycle. See also: Nuclear fuels; Plutonium; Thorium
Fuel preparation
Fissionable materials must be prepared for use in a nuclear reactor through mining, milling, conversion, enrichment, and fabrication.
Mining
The nuclear fuel cycle begins with the mining of uranium or thorium. Uranium is estimated to be present in the Earth's crust to the extent of 4 ppm (parts per million). The concentration of thorium is nearly three times greater. However, uranium and thorium are so widely distributed that significant concentrations in workable deposits are more the exception than the rule. Exploitable deposits have on average a concentration of 0.1–0.5% of uranium oxide (U3O8) by weight.
Large deposits of uranium-rich minerals are found in many places, with the most extensive mining having taken place historically in countries including Australia, Canada, Germany, Kazakhstan, Niger, Russia, South Africa, and the United States.
The chief sources of thorium are coastal sands rich in monazite along India’s eastern and southeastern coasts, with significant reserves in the Rocky Mountains in the United States, along with Australia and Canada.
Milling
After uranium ore has been mined, it is crushed and the host rock separated from the core, usually by a flotation process. The uranium is milled and concentrated as a uranium powder, principally U3O8, which is generally known in the industry as yellowcake because of its color.
Conversion
The yellowcake is then shipped to a conversion plant, where it is oxidized to uranium oxide and then is fluorinated to produce uranium hexafluoride (UF6). This is a convenient form for the gaseous diffusion enrichment process, because the uranium hexafluoride sublimates (passes directly from the solid phase to the gaseous phase without liquefying) at 53°C (127°F).
Enrichment
The uranium hexafluoride, familiarly called hex, is shipped in tanklike containers to an enrichment plant. Gas centrifuges are widely used for enrichment. After enrichment, the two resulting streams—enriched uranium and depleted uranium—part company. The depleted uranium may be stored adjacent to the enrichment plant, and the enriched material is converted back to an oxide—this time, uranium dioxide (UO2)—and sent to a fuel fabrication plant. See also: Isotope separation
Fabrication
At the fabrication plant, uranium dioxide intended for light-water reactor fuel is shaped into cylindrical pellets, usually about 15 mm (0.6 in.) long and 10 mm (0.4 in.) in diameter. The pellets are sintered, that is, baked, to obtain a hard, dense consistency. After polishing, they are loaded into tubes made of Zircaloy, an alloy of zirconium. A number of tubes are put together with appropriate tie plates, fittings, and spacers to form fuel assemblies. See also: Zirconium
Fuel loading and reactor operations
Completed fuel assemblies are shipped from the fuel fabrication plant to the power plant in criticality-proof containers and on arrival are stored in a clean-fuel vault. At refueling time, a polar crane at the top of the reactor containment building eases the vessel head off. The reactor cavity—the concrete pit in which the reactor vessel is moored—is filled with water to a height such that full-length (usually 4-m or 12-ft-long) fuel assemblies lifted out of the core can swing clear of the lip of the reactor vessel without coming out of the water. The purpose of the water is to shield the workers from the radiation of the used fuel assemblies. Those fuel assemblies removed are lowered into a canal that connects the reactor cavity with the spent-fuel pool. Storage racks within the spent-fuel pool are made of a metal containing enough neutron poisoning material to make certain that the spent assemblies in the pool cannot go critical there.
The assemblies not ready for discharge are shuffled, that is, their position is rearranged in the core, and the fresh clean assemblies are then loaded into the core grid spaces freed. Underwater periscopes are provided for use in the reactor vessel and in the spent-fuel pool as required. Assemblies discharged are inspected visually by means of these periscopes to check their condition. The radioactive content of the water is also checked to make certain that none of the fuel rods has developed any pinhole leaks that could permit release of fission products into the water. See also: Periscope
A neutron source is used to permit close monitoring of the start-up process by external neutron detectors. This source, usually an antimony or a polonium-beryllium capsule, emits a large number of neutrons spontaneously and is lowered into the core through a guide tube while the control rods are slowly and carefully retracted. Radiation monitors around the core report remotely to the control room the neutron flux as it increases. Flux is the number of neutrons crossing a unit area per unit time and is proportional to the fission reaction rate. Once the reactor has become critical, the control rods are retracted further to increase power until the reactor is at 100% power.
Spent-fuel storage and transportation
A large commercial reactor core holds around 250 fuel assemblies. Because nuclear power plants provide base load to the electric grid, refueling outages are preferably timed to occur in the spring or fall, when electricity demand is lower. The predominant fueling strategy requires that either one-third or one-fourth of the fuel assemblies be discharged from the core every 18 to 24 months. While fresh assemblies are placed in the core to replenish its reactivity, the spent fuel is transferred to an adjacent pool where it is stored for several years. Spent fuel is highly radioactive, and the water serves as shielding and as a cooling medium, to remove the heat produced by the decaying fission products. After several years of cooling in the spent-fuel pool, the assemblies are suitable for temporary dry-cask storage or, where available, transportation to a reprocessing plant. See also: Spent nuclear fuel disposition
Reprocessing and refabrication
At the reprocessing center, the spent-fuel rods are stripped of cladding, and the spent-fuel pellets are dropped in a pool of nitric acid in which they dissolve. The solution is then fed to countercurrent extraction systems. Usually, in the first extraction cycle about 99% of the fission waste products are removed. Then further purification and separation of the plutonium from the uranium is performed. The end products of this step are usually uranium dioxide and plutonium dioxide (PuO2), which can be recycled. Reprocessing of commercial fuel allows unfissioned fuel material to be returned to the inventory of material and reused for fuel fabrication. Commercial nuclear fuel is reprocessed in countries including France, Japan, and Russia. Commercial fuel reprocessing activities were discontinued in the United States in 1977. See also: Nuclear fuels reprocessing
Radioactive waste management
Fission waste products are removed from a reprocessing plant and disposed of in various ways. High-level waste can be concentrated into a glassy bead form and either buried in salt beds deep in the Earth or shipped to a heavily guarded disposal site. Low-level wastes are stored in liquid or solid form.
Management of low-level wastes generated by the nuclear energy industry requires use of burial sites for isolation of the wastes while they decay to innocuous levels. Other radioactive wastes, such as those from medical procedures and industrial applications, equal or exceed these from nuclear power plants. Operation of commercial burial sites is subject to regulations by federal and state agencies.
Routine operations of nuclear power stations result in very small releases of radioactivity in the gaseous and water effluents. The U.S. Nuclear Regulatory Commission has adopted the principle that all releases should conform to the “as low as reasonably achievable” (ALARA) standard. ALARA guidance has been extended to other portions of the nuclear fuel cycle. See also: Radioactive waste management
Decommissioning of nuclear plants
To date, more than 100 commercial power reactors have been decommissioned, along with dozens of prototype reactors and more than 250 research reactors. Decommissioning requires several steps: assessments and characterization of the hazards, environmental review, engineering, dismantling and decontamination of the plant, and finally remediation. The process requires that the plant be maintained cost-effectively, safely, and securely while it awaits decommissioning, and that the site and buildings be made available for reuse following decommissioning (if practical).
For decommissioning, the International Atomic Energy Agency (IAEA) has defined three options: Immediate Dismantling (known as Decon in the United States), Safe Enclosure (Safstor), and Entombment (Entomb). Immediate dismantling requires that the equipment, structures, and portions of a facility and site containing radioactive contaminants be removed or decontaminated to a level that permits unrestricted use. Safe Enclosure is also called deferred dismantling, because it requires that the facility be placed and maintained in a condition that allows it to be safely stored and later decontaminated for unrestricted use, generally within 40–60 years of reactor shutdown. Entombment keeps radioactive materials on-site, encasing them in durable structures, such as concrete, to limit the threat of radiation escape or unauthorized access to the site.
Safety
Nuclear power facilities present a potential hazard that is rarely encountered with other facilities, that is, radiation. A major health hazard would result if, for instance, a significant fraction of the core radioactivity inventory of a power reactor were released to the atmosphere. Engineered safety systems, various construction and design codes, regulations on reactor operation, and periodic maintenance and inspection are relied on to limit this risk.
All reactors have engineered safety features, both active and passive, designed to prevent serious accidents and to mitigate them if they occur. A nuclear plant’s safety is achieved through a concept of “defense in depth.” This provides a series of protective barriers with redundancy at each level and for each active component, from the uranium dioxide fuel matrix’s high melting point (2760°C or 5000°F) and chemical stability, to the fuel cladding, to reactor coolant systems, and the strength of reactor containment buildings made of thick concrete shells lined with steel and heavily reinforced with steel bars. See also: Reinforced concrete
Nevertheless, accidents have occurred, most notably at the Chernobyl Nuclear Power Plant in Ukraine (then the Soviet Union) on April 26, 1986, and at the Fukushima Daiichi Nuclear Power Plant in Japan (Fig. 3) in March 2011. These events are the only two in history to have been classified on the International Nuclear and Radiological Event Scale, which was introduced by the International Atomic Energy Agency in 1990, as Level 7 events, described as “Major Accidents” with major releases of radioactive material.
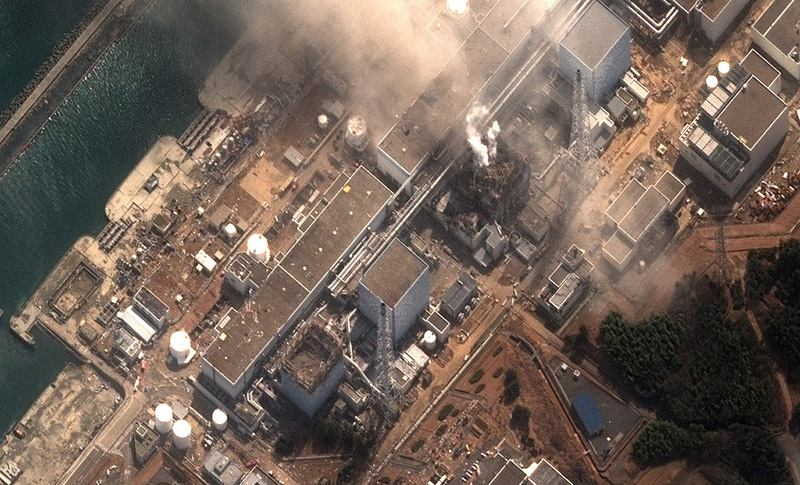
In brief, the Chernobyl accident occurred as a result of a failed test of a scenario involving the loss of primary electrical supply to the plant. Reactor design flaws and actions by plant personnel led to uncontrolled reactions, culminating in a steam explosion and fires that converted about 5% of the nuclear core into particles that went into the atmosphere and downwind—a total of 5200 petabecquerels (PBq) of iodine-131 equivalent. [The becquerel (Bq) is the SI unit of activity (radioactive disintegration rate).] Two workers died from injuries the night of the accident, while more than 200 people exhibited some degree of radiation poisoning; 28 of these people died in the following weeks as a result of their exposure. In the immediate region around the plant, some thyroid cancers in the decades after the accident have also been attributed to radioactive iodine fallout. Overall, the accident prompted a sweeping reappraisal of nuclear safety culture in the former Soviet Eastern Bloc.
In brief, the Fukushima Daiichi accident occurred because of a magnitude 9.0 earthquake on March 11, 2011, which generated a 15-m (49-ft) tsunami. This tidal wave knocked out the electrical supply and cooling mechanisms in place for multiple reactors at the Fukushima Daiichi plant. Within a few days, three reactor cores had melted down and containment was lost. The concomitant radiation release of about 940 PBq of iodine-131 equivalent did not result in any radiation poisonings or deaths. Approximately 100,000 people were temporarily evacuated from the region surrounding the stricken plant, though resettlement has proceeded slowly.
Outlook
In part because of these two nuclear accidents, but also because of high initial capital costs, nuclear plant construction has slowed in recent decades. Countries such as Germany have pledged to phase out nuclear power. With increasing emphasis being placed on clean and renewable energy sources in light of climate change, however, nuclear power’s advantage as a non-greenhouse-gas–producing power source suggests that it will continue to supply a significant portion of energy for human use. Currently, nuclear power provides about 20% of electricity generation in the United States and about 10% for the world.